Choosing the right fastener for the job can be overwhelming, given the myriad options available. But most consumers ask what’s the difference, between structural screws vs lag bolts when working with structural applications?
Both of these fasteners are designed for structural applications i.e. one that requires heavy load connectors, but here’s how they compare to each other, so you can decide which one is right for your project.
Lag Screw vs Lag Bolt
What’s the difference between lag screws vs lag bolts? There is no difference, they are known by both terms. Some people call them lag screws, other people call them lag bolts.
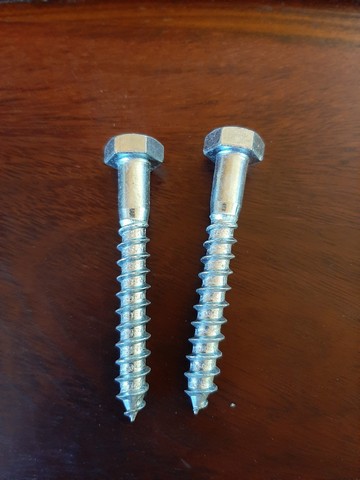
Some say that the difference between a bolt and a screw is that a bolt is turned from the outside of the head, using either a spanner or socket, while a screw is turned from within the head, using a screwdriver or something similar.
Others say that it has to do with nuts;
So a bolt has an external thread that is intended to be tightened by torquing a nut, whereas a screw has an external thread capable of mating with a preformed internal thread or forming its own thread and being tightened by torquing the head.
In the US, there is a difference between screws and bolts which affects rates of taxation and is governed by the United States Customs and Border Protection. They have an interesting document titled “Distinguishing Bolts from Screws”.
If you’ve got nothing better to do, then you could have a read of it and be none the wiser!
It’s a bit like the correct tire pressure argument, everybody has his own opinion!
I’m sure that when you go to the hardware store and ask for either lag bolts or traditional lag screws, the guy at the counter is going to know what you’re looking for.
What are Structural Screws?
Structural screws, also referred to as construction screws are a new type of screw that offer superior fastening power. They are typically made from super strong, heat treated galvanized steel, and are often a preferred alternative to lag bolts, as they greatly reduce time and effort put into drilling.
Furthermore, structural screws showcase greater strength and allowable loads than larger dimensional fasteners and can handle a shear strength between 250 lbs to 400 lbs. With structural screws, you do not have to drill pilot holes, but you can simply drive them in with most decent cordless drill/drivers. The hex head avoids the problem of stripped heads.
Apart from traditional hex-head drives, structural screws are also available in Torx (six contact points) or Spider (eight contact points) drive heads. These additional recessed contact points are designed to spread the driving torque, and reduce the chances of cam out that you’d experience with pozi heads or Phillips screwdrivers.

Even though structural screws are extremely thin and sharp, they are a great alternative to applications that use beefy screws. They allow you to skip the predrilling process, and get right to the driving, and are designed to meet stringent engineering standards. Structural fasteners prove handy in several different applications including:
- Structural decking
- Heavy duty framing
- LVL fastening
- Ledger boards
- Multi-ply
- Interior and exterior remodeling
A couple downsides of structural screws are that they are expensive, and only available from a limited number of brands of screw manufacturers such as GRK, Spax and FastenMaster. GRK screws are arguably some of the best available.
GRK structural screws – structural screws from GRK are regarded as the best in this segment, and are billed as an “easy to install lag alternative”. They feature a few unique traits such as a Zip-Tip — which provide faster penetration, W-Cut — for low installation that makes them easier to drive and install, a unique thread design, and drill flutes.
GRK structural screws are also Climatek coated, making them corrosion resistant in pressure treated wood with corrosive ground contact. The company offers several different varieties of construction screws including RSS Rugged Structural screw, and Joint and Truss structural screws for heavy duty floor and roof construction.
GRK also offers PHEINOX 305 Stainless Steel screws for use in corrosive environments such as boardwalks, deck projects and spas, and PHEINOX 316 Stainless Steel screws for use in harsh cold water environments such as deck substructures and agricultural areas.
Spax structural screws – these structural screws are German engineered and American made, and provide great tensile strength per fastener. Spax PowerLags feature the company’s patented thread technology, which eliminates the need to predrill, and can be driven faster than other structural screws.
PowerLags can be had in an array of screw head styles including hex head for optimal driver engagement, and T-Star head style for improved aesthetics, and unmatched clamping force. Other types of head styles offered by Spax include yellow zinc, coating options for interior applications, and HCR coating for exterior use. Flat Head Structural Screws are suitable for a wide range of wood types and framing applications.
FastenMaster Structural Screws — FastenMaster is a leading manufacturer of structural type wood screws, and offers several types to choose from including hex head structural screws, and multi-ply truss screws.
Any of the above can be used as a replacement for lag screws, but cost is generally the deciding factor here.
What Are The Best Structural Screws?
Some of the most popular structural screw brands today are;
There is probably not a best overall structural screw, but rather that would rest with different manufacturers for different products for different applications.
What is a Lag Bolt?
Lag bolts, often dubbed as lag screws have been around for many years, and are regarded as some of the toughest fasteners in the market. They are called lag bolts because they are considerably larger than other types of screws, with threads extended to part of the shaft.
This unthreaded area is located right below the screw head, and is an area of variable thickness. Even though this small area known as lag portion of the screw is unthreaded, it is what gives a lag bolt its magical properties by creating significant compressive forces in this part of the fastener.
This consequently result in most binding force between the two materials, which in turn allows them to resist more forces. Unlike structural screws, lag bolts are only available with hex heads, and installing them will require a nut driver and a rachet. But on the flipside, lag screws do require you to predrill two holes — one for the threads and other large one for the shaft.
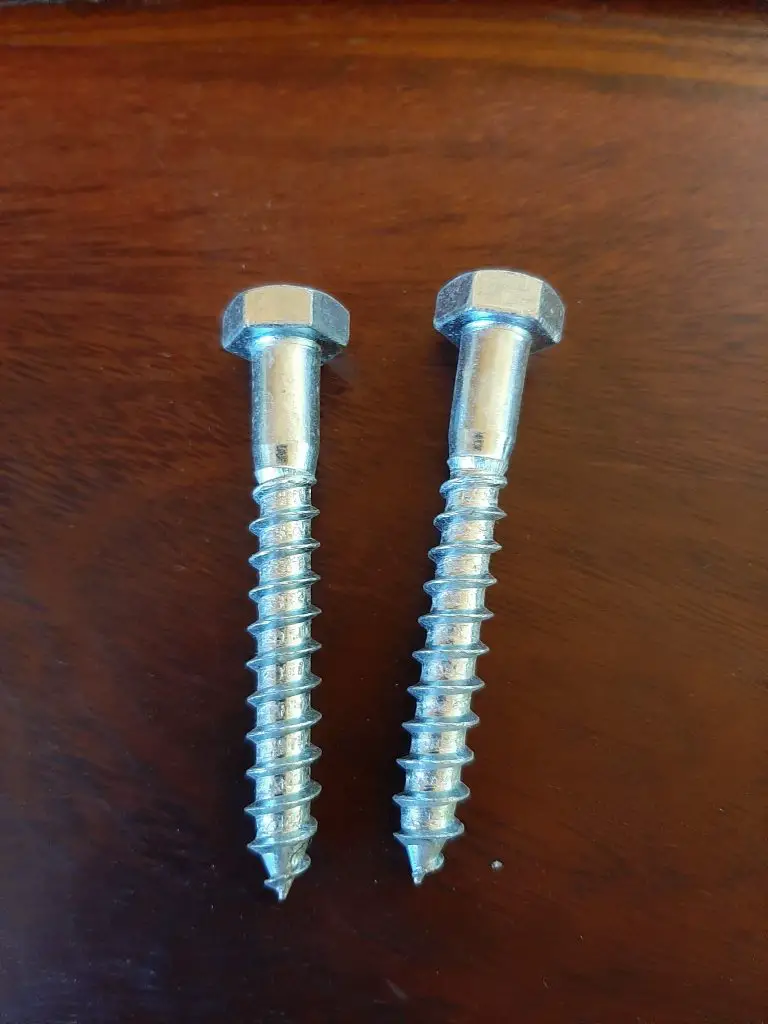
Apart from their exceptional strength and durability, lag bolts are a long lasting solution. They typically feature a robust carbon steel core with a galvanized zinc exterior, which protects the screws core from rust and corrosion. Lag bolts don’t generally rust or corrode, because moisture and oxygen can’t easily penetrate through the galvanized zinc.
In fact, when installed properly, lag screws can last a few decades, while offering an unrivalled level of stability to the objects on which they are used. Compared to structural screws, lag bolts are cheaper, so could be a cost efficient choice if you are working on a large scale project.
What Is a Lag Screw?
A lag screw, also known as a lag bolt, is an anchor bolt with a large, coarse threaded head designed to resist loosening and withdrawal from wood or other soft materials. This is accomplished by the large amount of surface area that is in contact with the surrounding material.
A lag screw can be used in wood, concrete, and masonry applications. Their heads are larger than common wood screws or bolts, and the threads are coarse to keep a grip in soft materials.
How to Use Lag Bolts?
1. The first most important step to using lag bolts properly is to align and clamp the two pieces of wood you want to join together.
2. Next, grab your drill, and with a drill bit that has the same diameter as the shank of the bolt drill through the first piece of wood only, without penetrating the second piece. To create a countersink hole to hide the head of the lag bolt, you can use a 1/2-inch Forstner bit and drill about 1/2 inch into the first hole you created.
3. Now drill into through the first hole and the second piece of wood using a 3/16-inch bit for softwood or a 7/32-inch bit for hardwood.
4. Lastly, insert the lag bolt into the hole, and drive it using a 3/8-inch socket. (If all else fails, refer to the manufacturer installation instructions!)
Final Thoughts on When To Use Structural Screws vs Lag Bolts
Deciding on when to use structural screws and lag bolts completely depends on the project you’re working on. Both types of fasteners provide long lasting connections, but one of the biggest differences is that lag bolts are time efficient per se since you have to drill pilot holes, and then ratchet the bolts in.
However, lag bolts are a cheaper solution, and may be worth considering if cost is a key factor in your project. But on the downside are more challenging to install, because you have to drill pilot holes first, and use two tools — a drill and a ratchet to drive them in, whereas structural screws can be driven easily with a screwdriver.
Last update on 2025-08-19 / Affiliate links / Images from Amazon Product Advertising API